In recent years, the automotive industry has seen a significant shift towards the use of aluminum in car body structure. This lightweight yet durable material offers numerous benefits, including improved fuel efficiency, enhanced performance, and better corrosion resistance. In this blog post, we’ll delve into the world of aluminium car body construction to understand why it has become a preferred choice for many automakers.
Innovations in Car Body Construction
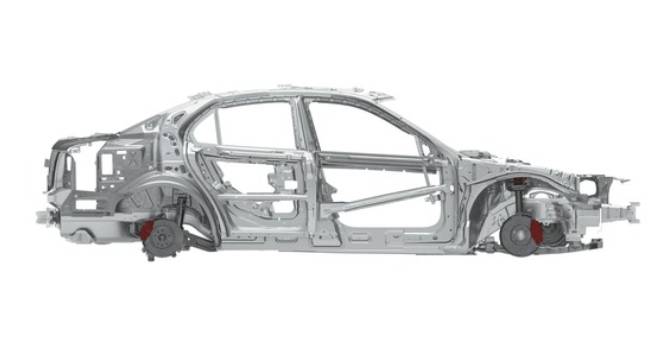
Evolution of Car Body Structure Materials
Before the emergence of aluminum car bodies, steel was the primary material used in car body structure. Traditionally, steel car bodies were assembled using stamped sheet parts and resistance spot welding. The industry underwent a significant transformation with advancements like hydroforming and laser beam welding. The introduction of high and ultra high strength steel grades led to enhancements in stiffness, crash worthiness, and weight reduction with minimal extra expenses. Notably, laser-welded continuous joints significantly increased the rigidity of monocoque body structures. The integration of structural elements crafted from thin hydroformed steel tubes further reinforced body strength and stiffness.
Transition to Aluminum Car Bodies
The shift towards all-aluminum car bodies involves applying similar design and manufacturing principles used in steel structures. However, mere material substitution may not always yield cost-efficient solutions. A holistic approach considering overall fabrication methods is essential. By embracing aluminum-oriented design concepts and tailored fabrication technologies, promising aluminium car body systems have emerged. The versatility of aluminum’s product forms – sheets, extrusions, and castings – offers a wide array of design possibilities, enabling substantial weight reduction and enhancing cost efficiency.
Design Concepts and Production Optimization
Selecting the most suitable product form based on car type and planned production volume is crucial for optimizing technical performance within economic and ecological constraints. Load-carrying profiles, stiffening sheets, and joining elements are fundamental components of a self-supporting car body structure. Aluminum’s advantages over steel, such as the availability of extruded profiles with complex cross-sections and thin-walled castings with excellent mechanical properties, provide innovative design solutions. The choice of the most effective aluminum body design concept depends on the envisaged production volume, with varying approaches for high-volume production focusing on cost efficiency and low-volume production emphasizing minimal capital expenditures.
Aluminium Car Body Construction
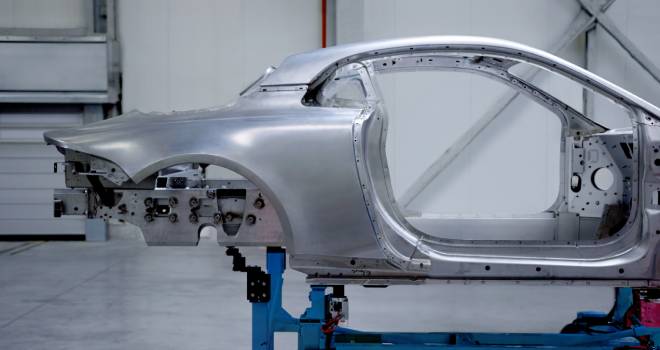
An aluminium car body structure typically consists of a combination of components, including the chassis, body panels, and other structural elements, all fabricated using aluminum alloys. Here is a breakdown of the key component that makes up an aluminium car body structure:
Aluminium Car Chassis
The chassis forms the backbone of the vehicle and provides the structural foundation for the entire car. In an aluminium car body, the chassis is often constructed using aluminum extrusions or castings to create a lightweight yet strong framework. The chassis supports the engine, suspension, and other key components of the vehicle.
Aluminium Body Panel
The outer shell of the car, including the door, hood, roof, and fender, is typically made from aluminum panels. These panels are manufactured using techniques like stamping or hydroforming to create the desired shapes and contours. An aluminum body panel offers weight savings compared to traditional steel panels while maintaining strength and durability.
Frame Component
Various frame components, such as cross member, subframe, and reinforcement, are also commonly made from aluminum in modern car designs. These components provide additional structural support and help distribute loads throughout the vehicle to enhance rigidity and crash safety.
Crash Management System
An aluminium car body is engineered with an integrated crash management system to improve occupant safety in the event of a collision. This system includes energy-absorbing structures, reinforced pillar, and crumple zone designed to deform in a controlled manner to dissipate impact energy and protect passengers.
Joining Method
Aluminum components in a car body structure are often joined using advanced techniques such as adhesive bonding, self-piercing rivet, and welding method like friction stir welding. This joining method ensures structural integrity and durability while minimizing weight and enhancing overall performance.
Integration of Component
An aluminium car body structure allows for the integration of various components into a single assembly to reduce weight and complexity. This integration may involve combining structural element with functional component like suspension mounting point or safety system to optimize space and improve overall efficiency.
Aluminium Car Chassis Design
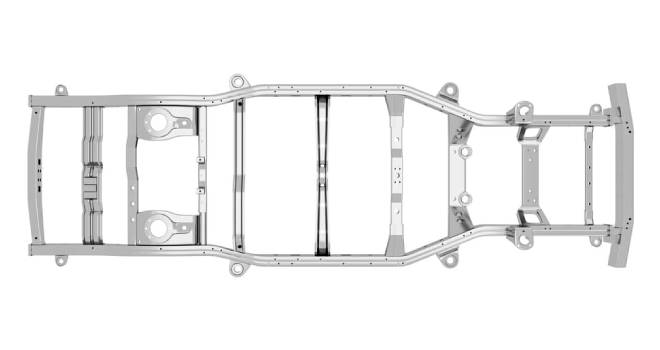
Design Variety Of Aluminium Car Chassis
Aluminium car chassis designs have seen significant advancements, offering a diverse range of options tailored to the needs of the automotive industry. These include aluminium sheet unibody structures, aluminium spaceframes, and lightweight body architectures with separate body shells. Each design emphasizes flexibility, efficiency, and modularity, making them particularly well-suited for low-volume production and specialized vehicle models.
Aluminium Sheet Unibody Structures
Aluminium sheet unibody structures represent a cutting-edge design approach where the chassis and body are integrated into a single unit. This design method involves using aluminium sheets of varying thicknesses that are stamped, formed, and welded together to create a unified structure. The unibody design enhances rigidity, reduces weight, and improves overall vehicle handling and crash safety. This construction style is often favored for mainstream vehicles due to its cost-effectiveness, efficient manufacturing process, and ability to accommodate various vehicle types.
Aluminium Spaceframes
Aluminium spaceframes are characterized by a structure composed of a series of interconnected tubes or extrusions that form a lightweight and rigid framework. These spaceframes are known for their high torsional rigidity and excellent strength-to-weight ratio, making them ideal for high-performance vehicles. The modular nature of spaceframes allows for customization and adaptation to different vehicle sizes and configurations. Additionally, the use of aluminium in spaceframes provides corrosion resistance and contributes to improved fuel efficiency due to reduced vehicle weight.
Lightweight Body Architectures with Separate Body Shells
Designs featuring lightweight body architectures with separate body shells combine an aluminium car chassis with a detachable body shell made from materials like aluminium, glass, or carbon fiber reinforced plastics. This approach allows for greater design flexibility, as the body shell can be easily replaced or modified without affecting the underlying chassis structure. The use of lightweight materials in the body shell reduces overall vehicle weight, enhancing performance and fuel efficiency. This design type is often favored for sports cars and high-end luxury vehicles where weight reduction and customization options are key considerations.
Best Aluminum For Car Body

As a prominent supplier of premium aluminum components, we offer top-quality aluminum car parts suitable for your vehicle’s body, encompassing elements such as the car chassis and more. Should you have any specific needs or inquiries, please do not hesitate to reach out to us. We are well-equipped to meet your requirements with excellence.