When it comes to working with aluminum sheet metal, shearing is a vital process that ensures precise cuts and shapes. In this comprehensive guide, we will delve into the world of aluminum sheet metal shearing, covering everything you need to know to master this essential technique.
What Is Shearing In Sheet Metal?
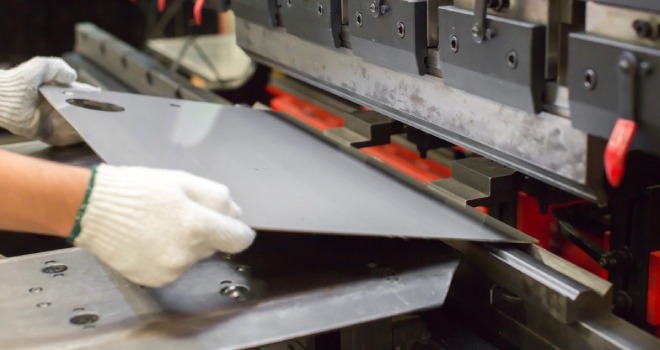
Shearing in sheet metal involves utilizing a punch (the moving blade) to press the material against a die (the fixed blade), creating localized shear stresses. This pressure continues until the material reaches its breaking point, resulting in a clean tear. One significant advantage of this method is the absence of chips formation, eliminating the need for material burning or melting. For a process to be considered shearing, the cutting blades must be straight; curved blades signify a different operation type, such as blanking, piercing, roll slitting, and trimming. Shearing is also known as die cutting, while terms like clicking, dinking, and kiss cutting are used less frequently in metalworking. Commonly sheared materials include sheet metal, plates, rods occasionally, and other materials like paper, plastics, and leather.
Differences Between Aluminium Shearing And Other Cutting Processes
Aluminium shearing is a cutting process that involves the use of straight cutting blades to make straight-line cuts on flat sheet metal. Here are some key differences between shearing and other cutting processes:
Shearing vs. Sawing:
- Shearing: In aluminium shearing, two blades come together to make a cut, producing a straight edge. It is ideal for cutting sheet metal.
- Sawing: Sawing involves a blade moving back and forth or in a circular motion to cut through materials. It is more commonly used for cutting larger or thicker materials.
Shearing vs. Laser Cutting:
- Shearing: Shearing is a mechanical cutting process that does not involve heat. It is suitable for cutting sheet metal with straight cuts.
- Laser Cutting: Laser cutting uses a high-powered laser to melt, burn, or vaporize material. It is precise and can cut intricate shapes but is more expensive than shearing for simpler cuts.
Shearing vs. Waterjet Cutting:
- Shearing: Shearing in sheet metal is a mechanical cutting process that relies on physical force to cut materials.
- Waterjet Cutting: Waterjet cutting uses a high-pressure stream of water mixed with an abrasive substance to cut through materials. It is versatile and can cut a wide range of materials, including metals, plastics, and composites.
Shearing vs. Plasma Cutting:
- Shearing: Shearing produces clean, straight cuts without the need for additional finishing processes.
- Plasma Cutting: Plasma cutting uses a high-velocity jet of ionized gas to cut through electrically conductive materials. It is faster than shearing but may require more finishing work.
Shearing vs. Punching:
- Shearing: Aluminium shearing involves two blades coming together to cut the material.
- Punching: Punching uses a punch and die to create holes or shapes in the material without cutting all the way through. It is commonly used for creating perforations or specific shapes in sheet metal.
Aluminum Sheet Metal Shearing Process
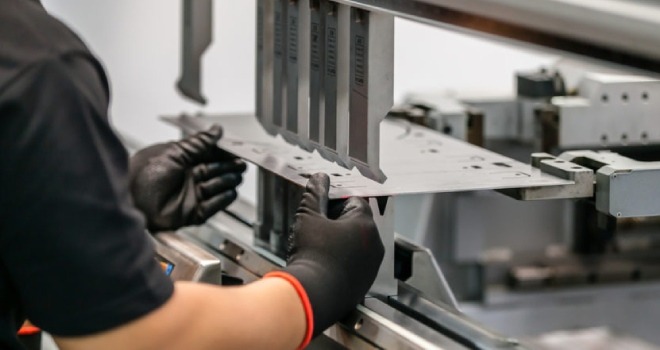
The aluminum sheet metal shearing process involves cutting aluminum sheets by employing a punch and die mechanism. Initially, proper preparation is key, ensuring the aluminum sheet is securely positioned for cutting. The shearing machine is then set up with the appropriate punch and die to execute the desired cut. Subsequently, the aluminum sheet is carefully positioned between the punch, which acts as the moving blade, and the die, serving as the fixed blade.
Upon activation of the shearing machine, the punch descends, exerting force on the aluminum sheet to cut through it. This action subjects the sheet to localized shear stresses between the punch and die until it reaches a breaking point, resulting in a clean cut along the intended length. Post-cutting, a thorough inspection of the edge ensures smoothness and accuracy, with any necessary adjustments made for precision. Following completion of the shearing process, the cut aluminum sheet is removed from the machine for further processing, which may include deburring or finishing to refine any rough edges left from the shearing action.
How To Caculate Aluminum Sheet Shearing Force?
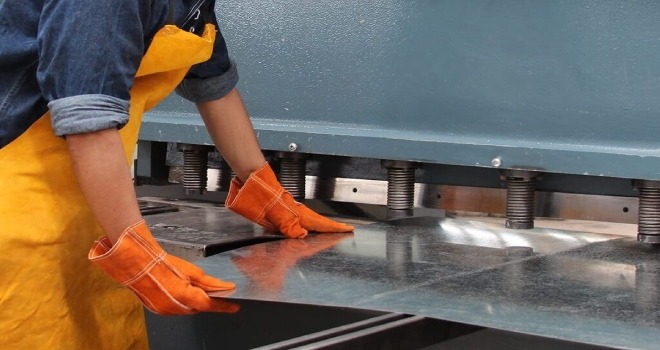
Determining the shear cutting force in the process of shearing aluminum sheets is critical for ensuring operational efficiency and safety. The shear cutting force is influenced by various factors such as the material’s strength, thickness, blade sharpness, shearing speed, and blade clearance.
The formula commonly used for calculating shear force is:
F=τ⋅A
Here:
- F represents the shear force,
- τ denotes the shear strength of the material, and
- A signifies the shear area, usually computed as the product of the plate thickness and the shearing length.
Understanding and computing the shear force aids in selecting the appropriate shearing equipment and optimizing process parameters for a smooth shearing operation and high-quality outcomes.
In the context of a guillotine shearing machine, frequently employed for cutting metal sheets, the required shearing force can be determined using specialized formulas like the Norshari Formula. This formula considers factors such as plate tensile strength, elongation ratio, plate thickness, cutting angle, and coefficients related to bending force, blade clearance, and material pressing.
For example, when calculating the cutting force for a 6061 aluminum plate of specific dimensions, the formula provides an estimate of the force needed. Adjustments might be necessary when working with different materials, such as stainless steel or other aluminum alloys, where appropriate multipliers are applied to the calculated force based on the material properties.
Aluminum Sheet Metal Shearing Advantages
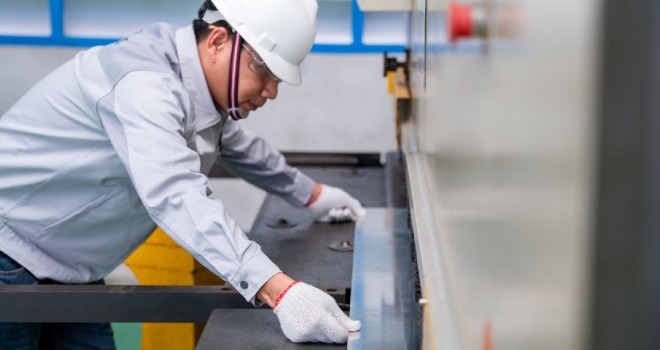
Shearing sheet metal offers several advantages due to the characteristics of the aluminum and the shearing process itself:
Clean Cuts: Shearing produces clean, straight cuts on aluminum sheets, providing precise edges without the need for additional finishing processes in many cases.
Efficiency: Shearing is a fast and efficient method for cutting aluminum sheets, making it ideal for high-volume production environments.
Cost-Effective: Compared to some other cutting methods, shearing is a cost-effective solution for cutting aluminum sheets, especially for large quantities.
Minimal Material Waste: Shearing sheet metal produces minimal aluminum waste, as the cut width is typically small, maximizing material usage and reducing scrap.
Versatility: Shearing can be used to cut aluminum sheets of various thicknesses, making it a versatile option for different project requirements.
Suitable for Thin Materials: Shearing is particularly effective for cutting thin aluminum sheets, providing precise cuts without distortion.
No Heat-Affected Zone: Unlike some thermal cutting methods, sheet metal shearing does not introduce a heat-affected zone, preserving the material properties of the aluminum sheet.
Ease of Operation: Shearing machines are relatively easy to operate and maintain, making them accessible for a wide range of users.
Scalability: Shearing can be easily scaled for small-scale operations as well as large industrial applications, offering flexibility in production.
Strength Retention: Shearing maintains the inherent strength of aluminum sheets along the cut edges, ensuring structural integrity in the finished products.
Overall, the advantages of shearing sheet metal make it a preferred cutting method for many applications where precision, efficiency, cost-effectiveness, and minimal aluminum waste are essential considerations.