Transformers are crucial components in electrical systems, responsible for stepping up or stepping down voltage levels for efficient power transmission and distribution. The choice between aluminum and copper for transformer windings is a critical decision that influences the transformer’s efficiency, cost, and overall performance.
Copper vs. Aluminium Conductivity
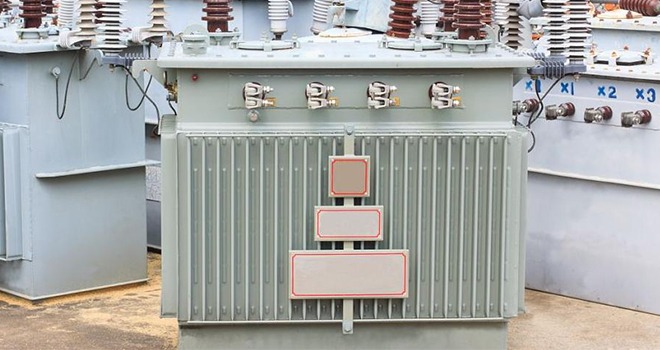
In comparing copper and aluminum conductivity in transformers, it’s crucial to note that aluminum exhibits 61% of the conductivity of copper while weighing just 30% of copper’s weight. This means that an aluminum wire with the same electrical resistance as copper would weigh only half as much.
The conductivity of copper, being higher than that of aluminum, results in lower resistivity and reduced energy losses in transformer operations. Copper’s superior conductivity enhances efficiency and performance in transformers compared to aluminum, which has lower conductivity and higher resistivity, leading to increased energy losses during operation.
Aluminum vs. Copper: Weight And Size
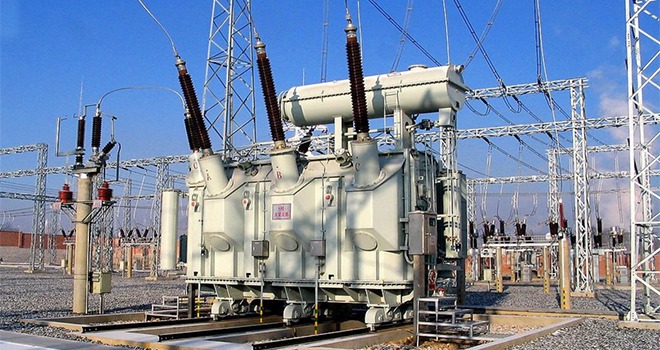
Aluminum’s substantial weight advantage over copper is pivotal in transformer applications, particularly for ease of handling and transportation. This characteristic is especially critical in large power transformers where reducing the overall weight is essential for logistics and installation purposes. Conversely, copper’s higher density enables more compact transformer designs, offering advantages in installations with limited space availability. The decision between aluminum and copper windings in transformers hinges on striking a balance between weight considerations for transportation and handling efficiency, and space constraints where a smaller footprint is required for installation.
How Weight Impact Transfomer
The weight of a transformer plays a crucial role in various aspects of its performance and installation:
Handling and Transportation: The weight of a transformer affects how easily it can be transported and maneuvered during installation. Lighter transformers, such as those with aluminum windings, are easier to handle and transport, reducing the logistical challenges and costs associated with moving heavy equipment.
Installation: The weight of a transformer influences the requirements for its foundation and support structures. Heavier transformers may necessitate more robust foundations to bear the weight and ensure stability during operation. Lighter transformers offer flexibility in placement and installation options.
Space Constraints: The weight of a transformer can impact the size and layout of the installation site. Lighter transformers, like those with aluminum windings, are advantageous in space-constrained environments where minimizing the footprint of the equipment is essential.
Aluminum vs. Copper: Performance In Transfomer
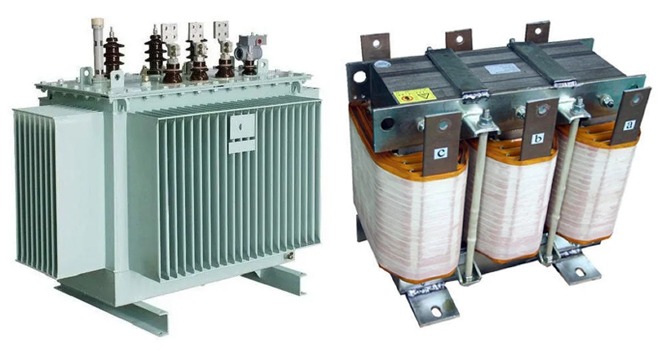
In transformer windings, both aluminum and copper have distinct advantages based on their properties and performance characteristics:
Aluminum In Transformers
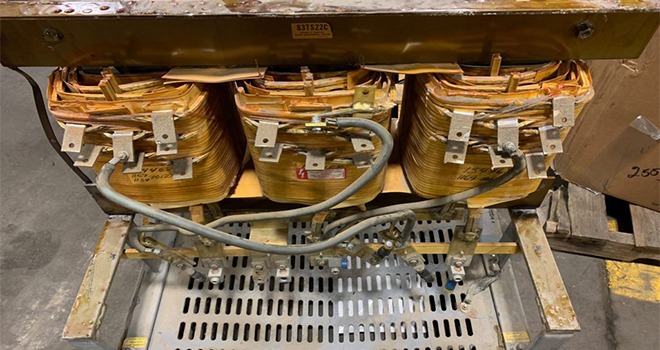
Advantages Of Aluminum Transformers
Greater Heat Storage: Aluminum windings can store approximately 2.3 times more heat per pound compared to copper windings during short-time overloads.
Dramatic Eddy Current Reduction: Aluminum windings significantly reduce eddy currents in wire wound transformers, improving efficiency.
Better Harmonic Management: Aluminum’s greater surface area helps the transformer winding handle excess heat caused by harmonics more effectively.
Less Mechanical Stress: Aluminum’s flexibility allows it to conform better to winding shapes, reducing mechanical stress during application.
Exterior Oxidization: Aluminum oxidizes only where exposed to air, providing better resistance to oxidation compared to copper.
Stable Pricing: Historically, aluminum pricing has been more stable, aiding cost forecasting in transformer manufacturing.
Disadvantages of Aluminum in Transformers
- Greater Electrical Connection Difficulty: Aluminum’s higher thermal expansion rate and tendency to oxidize make creating airtight electrical connections more challenging, requiring extra precautions and manual work.
- Additional Material Required: Due to larger wire sizes needed for aluminum’s electrical properties, transformers with aluminum windings may require more material, potentially leading to larger transformer sizes that could pose space constraints.
- Additional Maintenance: Transformers with aluminum windings typically necessitate more maintenance due to aluminum’s quicker oxidation rate compared to copper.
Copper In Transformers
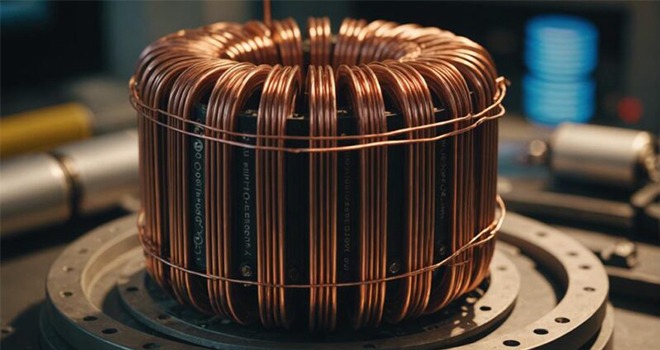
Advantages Of Copper Transformers
- Less Material Required: Due to its high conductivity, copper wire sizes are smaller, resulting in smaller transformers ideal for space-constrained installations.
- Easier Electrical Connections: Copper’s properties make electrical connections simpler and more reliable compared to aluminum.
- High Electrical Conductivity: Copper offers superior electrical conductivity, enhancing energy efficiency in transformer operations.
- Less Maintenance and Easier Manufacturing: Copper windings facilitate easier manufacturing processes and require less maintenance over time compared to aluminum.
- Resistance to Oxidation: Copper exhibits greater resistance to moisture-corrosion and oxidation, maintaining reliability in various environments.
Disadvantages of Copper in Transformers
Complete Oxidation: Copper undergoes complete oxidation similar to steel, leading to faster deterioration when oxidation starts, unlike aluminum which only oxidizes on exposed surfaces.
Volatile Cost: The cost of copper can fluctuate significantly, posing challenges in cost forecasting and potentially affecting the overall cost-effectiveness of transformer production.
Is Aluminum Or Copper A Better Conductor In Transformer?
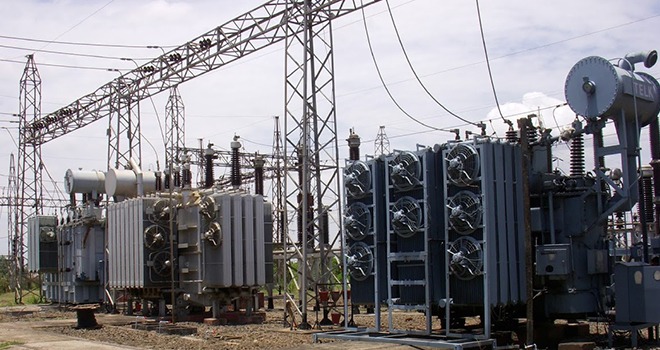
Copper outperforms aluminum in both electrical and thermal conductivity. However, as conductor sizes increase, the thermal performance gap between copper and aluminum narrows. Enhanced thermal conductivity in copper contributes to better short-circuit performance, vital in transformer operations. Aluminum, despite its lower conductivity, offers advantages in weight and cost savings, making it a preferred choice in scenarios where weight reduction and cost efficiency are crucial considerations in transformer design and operation.