Aluminum is a remarkable material known for its versatility, lightweight nature, and resistance to corrosion. These qualities have made it a top choice across various industries. One crucial aspect to consider when working with aluminum is the distinction between aluminum sheet and aluminum plate.
Aluminum Sheet vs. Plate: Thickness

When comparing aluminum sheets and plates, the critical distinction lies in their thickness:
- Aluminum Sheet: Characteristically thinner, with a thickness range from 0.008 inches (0.2 mm) to 0.25 inches (6.35 mm).
- Aluminum Plate: Notably thicker, typically commencing at 0.25 inches (6.35 mm) and extending up to 6 inches (150 mm) or beyond.
Impact of Thickness on Aluminum Sheet and Plate Strength & Durability
The thickness of aluminum sheets and plates significantly impacts their strength and durability. Thinner aluminum sheets, known for their flexibility and ease of shaping, are favored in weight-sensitive sectors like automotive and aerospace. However, they may exhibit lower structural strength compared to their thicker counterparts.
Thicker aluminum plates are inherently sturdier and more resistant to bending or deformation, offering higher load-bearing capacity. These plates are commonly employed in structural applications where strength is paramount, such as in heavy machinery and construction.
In terms of durability, thinner aluminum sheets, while lightweight and versatile, are more susceptible to damage from impacts. In contrast, thicker aluminum plates provide enhanced durability and resilience to wear and tear, making them ideal for applications requiring longevity and robustness, such as in structural components and machinery.
Aluminum Sheet vs. Plate: Manufacturing Process
In the manufacturing process of aluminum sheet and plate:
Aluminum Sheet
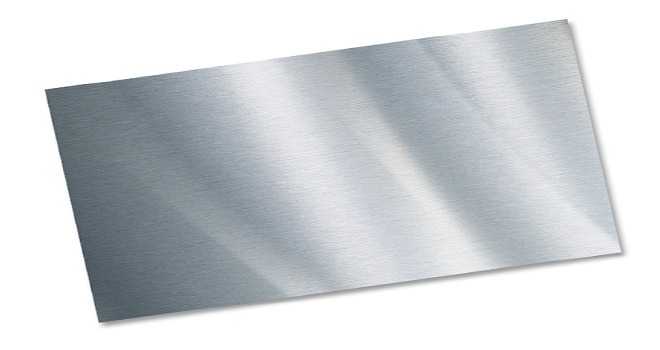
An aluminum sheet is typically produced through a method known as continuous casting and rolling. This process involves casting molten aluminum into an ingot, which is then rolled between pairs of rolls multiple times to gradually reduce the thickness until the desired gauge is achieved. The rolling process ensures the sheet has a uniform thickness and a smooth surface finish, making it suitable for various applications.
Aluminum Plate
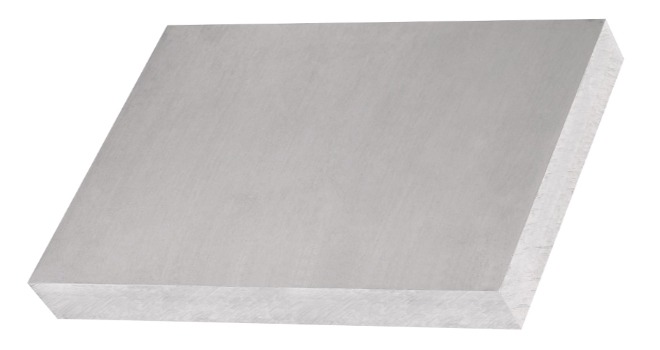
An aluminum plate is manufactured using a technique called direct chill casting. In this process, molten aluminum is poured into a large mold to create a thick slab. The slab is then heated to a specific temperature to enhance workability, rolled to the required thickness, and ultimately cut into a plate with specific dimensions. The direct chill casting method enables the production of thick aluminum plates with a consistent grain structure and excellent mechanical properties, making them ideal for heavy-duty applications in industries such as aerospace, marine, and construction.
Aluminum Sheet vs. Plate: Weldability
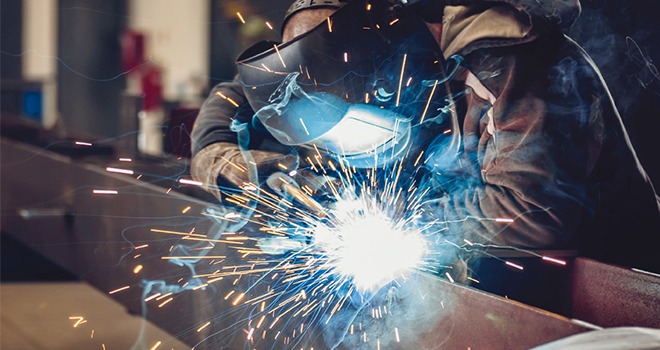
Welding Aluminum Sheet Metal
An aluminum sheet is generally easier to weld due to its thinner profile, making it suitable for various welding techniques such as MIG or TIG welding. The reduced thickness allows for quicker heat transfer during welding processes, facilitating techniques like MIG welding for efficient joining. TIG welding, known for its precision, is also commonly used on aluminum sheets to achieve intricate welds and maintain aesthetic quality.
When welding an aluminum sheet, it is essential to consider factors like surface cleaning to remove oxidation, selecting compatible filler materials, and adjusting welding parameters based on the specific thickness and alloy type being welded. Shielding gases like argon or helium are crucial to prevent atmospheric contamination of the weld pool.
Welding Aluminum Plate
An aluminum plate, with its increased thickness compared to a sheet, requires specialized welding techniques and equipment to ensure strong and reliable joints for structural integrity. Processes such as gas tungsten arc welding (GTAW) or shielded metal arc welding (SMAW) are commonly used for welding aluminum plates due to their ability to penetrate deeply and produce high-quality welds on thicker materials. These techniques offer better control over heat input, ensuring proper fusion and reducing the risk of defects like porosity.
Welding an aluminum plate involves considerations such as preheating to minimize distortion, selecting appropriate welding parameters for the thickness, and designing joints to enhance weld strength. Post-weld treatments like stress relief or heat treatment may also be necessary to address residual stresses and improve overall weld quality.
Shop Aluminum Sheet And Plate Now
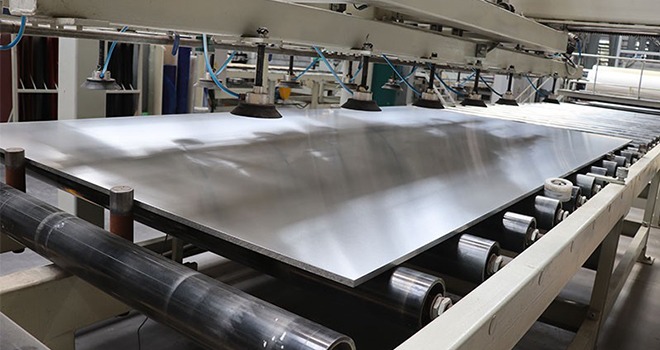
Discover our range of aluminum sheet and plate offerings at Aluminum Land, a leading manufacturer of premium aluminum products. Our expertly crafted aluminum sheets and plates are designed for a multitude of projects, ensuring exceptional quality and performance every time. Using top-grade aluminum, including marine-grade, aircraft-grade, and automotive aluminum, we cater to diverse industry requirements.
At Aluminum Land, we provide a wide selection of aluminum sheet and plate sizes to accommodate your specific needs. Whether you require materials for marine applications, aerospace projects, or automotive components, we have you covered. Get in touch with us today to explore our comprehensive range of high-quality aluminum products. Elevate your projects with Aluminum Land’s superior aluminum sheet and plate options.